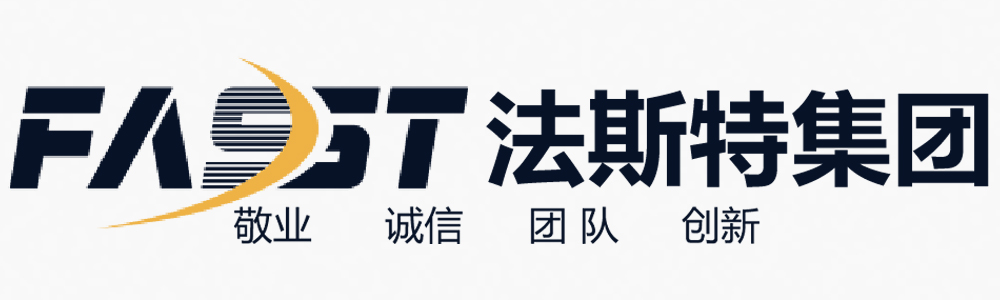
在硅胶制品的生产过程中,硫化工艺是决定产品质量的关键环节。然而,在实际操作中,常常会遇到性能不稳定的问题,这不仅影响产品的最终质量,还可能带来额外的成本损耗和交付延迟。本文将深入分析硅胶硫化工艺中常见的性能不稳定现象及其原因,并提出相应的解决方案。
硅胶是一种具有优异耐高温、耐低温、绝缘性好等特点的材料,广泛应用于电子、医疗、汽车等领域。硫化工艺是通过化学交联反应使硅胶从线性结构转变为三维网络结构的过程,从而赋予其稳定的物理和化学性能。常见的硫化方法包括过氧化物硫化、铂金催化硫化和缩合型硫化等。
然而,在实际生产中,由于原材料批次差异、环境因素或设备参数控制不当,可能导致硫化后的产品性能不稳定,如硬度不均、拉伸强度下降、回弹性能变差等问题。
在同一生产批次内,部分产品硬度明显高于或低于目标值。这种现象通常与硫化剂添加量不准确有关。例如,过氧化物硫化时,如果硫化剂计量不足,则会导致交联度不够,产品偏软;反之,若硫化剂过量,则会使产品过硬且易脆裂。
拉伸强度是衡量硅胶材料抗拉能力的重要指标。当硫化不充分时,材料内部交联密度较低,导致拉伸强度显著下降。此外,若硫化温度过高或时间过长,可能会引起材料老化,进一步削弱其力学性能。
回弹性反映了硅胶材料的形变恢复能力。若硫化过程中未达到最佳条件(如硫化温度偏低或催化剂失效),则可能导致交联点分布不均匀,从而影响回弹性能。
部分硫化后的硅胶制品可能出现气泡、裂纹或粘模等表面缺陷。这些问题往往源于脱模剂使用不当、模具清洁不到位或硫化过程中排气不良等原因。
硅胶原料的质量直接影响硫化效果。不同批次的硅胶可能存在分子量分布不一致、杂质含量超标等问题,进而影响硫化反应的效率。
硫化剂的添加量需严格控制。一旦比例失调,可能导致交联程度不足或过度交联,从而引发性能问题。
温度、湿度和压力等外部条件对硫化过程至关重要。例如,温度过高可能加速硫化反应,但同时也可能引发副反应;而温度过低则会导致硫化不完全。
现代硫化设备需要精确控制温度、时间和压力等参数。如果设备老化或校准不及时,容易造成硫化条件偏离设定值。
操作人员的经验和技术水平直接影响硫化工艺的执行效果。缺乏经验的操作人员可能无法及时发现并纠正潜在问题。
建立严格的原材料验收制度,确保每批硅胶原料的质量一致性。同时,建议采用高纯度的硫化剂和助剂,减少杂质对硫化反应的影响。
使用自动化程度高的硫化设备,并定期校准温度传感器、压力计等关键部件。针对不同型号的硅胶材料,制定详细的硫化曲线,确保每次硫化都能在最优条件下进行。
硫化车间应保持恒温恒湿,避免外界干扰。此外,定期清理模具,确保脱模剂涂抹均匀,有助于提升成品外观质量。
定期组织技术培训,提高操作人员的专业技能。同时,鼓励团队成员分享实践经验,形成良好的学习氛围。
硅胶硫化工艺中的性能不稳定问题并非不可克服,只要从原材料、设备、工艺和人员等方面入手,采取针对性措施,就能有效改善这一状况。未来,随着智能化制造技术的发展,相信硅胶硫化工艺的稳定性将进一步提升,为各行业提供更加优质的材料支持。
公司:惠州市法斯特精密部品有限公司
地址:龙门县惠州产业转移工业园北片区园区大道5号惠州市法斯特科技产业园区2号厂房四-五楼
Q Q:18665211415
Copyright © 2002-2024