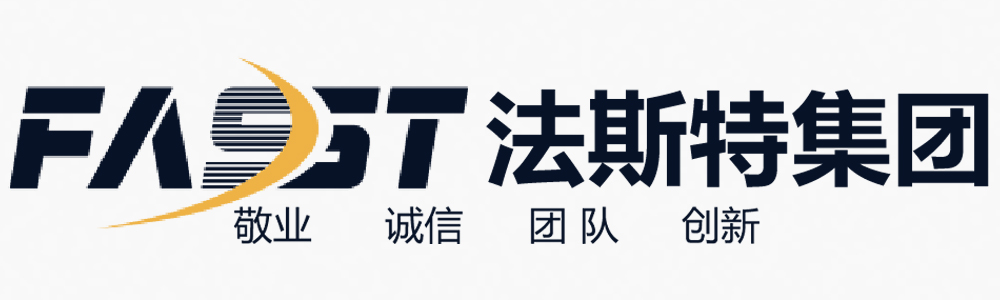
硅胶作为一种高性能的材料,在各种应用领域中得到了广泛的应用。然而,硅胶挤出过程中存在的问题常常限制了其生产效率和产品质量。本文将探讨如何通过一系列优化措施来实现高效且稳定的硅胶挤出。
硅胶挤出过程中常见的问题包括:产品尺寸不稳定、表面质量差、生产速度慢等。这些问题不仅影响最终产品的性能,还增加了生产成本,降低了企业的竞争力。要解决这些问题,必须从设备、工艺、原材料等多个方面入手,进行全面的优化。
选择合适的挤出机是保证硅胶挤出效果的第一步。不同类型的挤出机适用于不同的硅胶类型和生产需求。例如,对于高粘度的硅胶,应选择具有较高螺杆转速和强大驱动能力的挤出机。此外,设备的加热系统也非常重要,它直接影响到硅胶的流动性和挤出稳定性。
先进的控制系统能够实时监控和调整挤出过程中的关键参数,如温度、压力和速度。这些参数的稳定控制对确保产品质量至关重要。例如,采用闭环反馈控制系统可以实时调整挤出机的工作状态,从而减少波动,提高产品的均匀性和一致性。
原材料的质量直接影响到最终产品的性能。因此,进行适当的预处理是非常必要的。这包括原材料的筛选、混合以及干燥等步骤。优质的原材料不仅可以提高挤出效率,还能改善产品的物理和化学性质。
合理的工艺参数设定对于实现高效挤出同样重要。例如,合适的挤出温度和速度可以显著提高生产效率,同时保证产品质量。过高的温度可能导致硅胶分解,而过低的温度则会增加能耗并降低生产效率。因此,需要根据具体的硅胶类型和生产工艺来进行精确的参数设定。
在线检测技术能够在生产过程中实时监测产品的尺寸、形状和表面质量等关键指标。这种即时反馈有助于及时发现并解决问题,从而避免不合格品流入市场。例如,利用激光扫描仪或视觉检测系统可以快速准确地评估挤出产品的质量。
后处理工艺主要包括冷却、切割和包装等步骤。有效的后处理不仅可以改善产品的外观,还可以进一步提升其性能。例如,适当的冷却方式可以防止产品变形,而精确的切割则有助于保持产品的一致性。
以某企业为例,该企业在硅胶挤出过程中遇到了尺寸不稳定的问题。通过对设备的升级改造,引入了先进的控制系统,并优化了原材料预处理和工艺参数设定。经过一系列改进措施,不仅提高了生产效率,还将产品的尺寸稳定性提高了50%以上,大大提升了企业的市场竞争力。
综上所述,通过设备优化、工艺优化以及严格的质量控制,可以有效解决硅胶挤出过程中存在的问题,实现高效稳定的生产。未来,随着技术的不断进步,相信硅胶挤出工艺将会变得更加先进和完善,为各行业的发展提供强有力的支持。
本文通过对硅胶挤出过程中常见问题的分析,提出了设备优化、工艺优化及质量控制等方面的解决方案,旨在帮助企业和研究机构提高硅胶挤出效率和产品质量。希望本文能为相关领域的工作者提供有益的参考。
公司:惠州市法斯特精密部品有限公司
地址:龙门县惠州产业转移工业园北片区园区大道5号惠州市法斯特科技产业园区2号厂房四-五楼
Q Q:18665211415
Copyright © 2002-2024