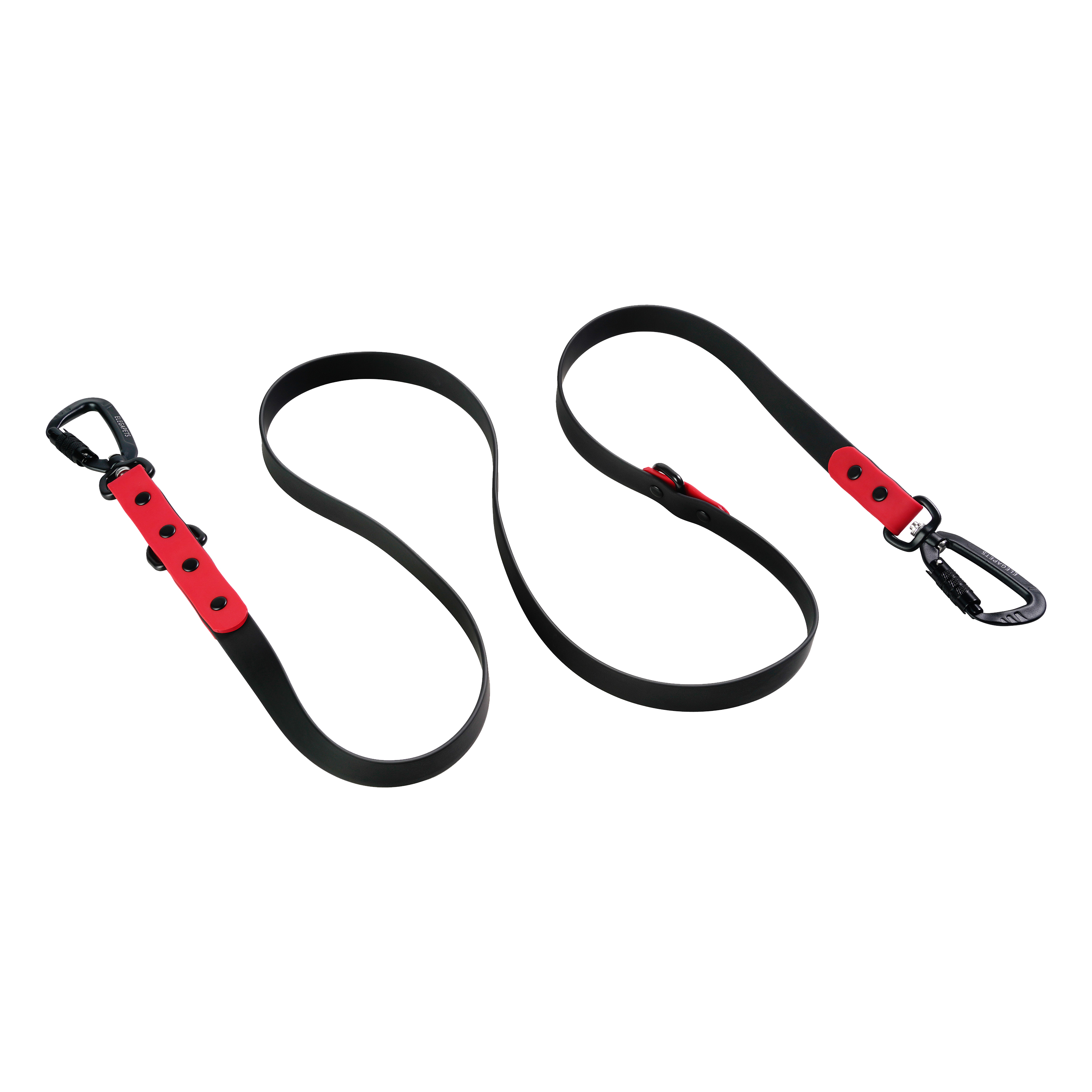
硅胶挤出:实现高效挤出的解决方案
硅胶材料因其卓越的耐温性、化学稳定性和生物相容性,在各种工业应用中备受青睐。然而,硅胶的加工难度较高,尤其是挤出工艺,需要精确控制温度、压力和速度等参数。本文将探讨如何通过优化设备、工艺流程和材料选择来实现高效硅胶挤出。
一、设备选择与优化
选择合适的挤出机是实现高效硅胶挤出的关键。硅胶挤出机通常包括以下几种类型:
- 单螺杆挤出机:适用于低粘度硅胶材料,结构简单,成本较低。
- 双螺杆挤出机:能够提供更好的混合效果,适合高粘度硅胶材料,且能提高生产效率。
- 柱塞式挤出机:适用于形状复杂或尺寸精度要求高的产品。
为了提高挤出效率,应考虑以下因素:
- 加热系统:确保均匀加热,避免局部过热导致硅胶分解。
- 冷却系统:快速冷却以减少硅胶在模具中的停留时间,提高生产速度。
- 控制系统:采用先进的PLC控制系统,实现对温度、压力和速度的精确控制。
二、工艺流程优化
硅胶挤出工艺流程主要包括以下几个步骤:
- 原料准备:根据所需产品的性能要求,选择合适的硅胶材料,并进行预处理,如脱气、过滤等。
- 混炼:将硅胶与填料或其他添加剂混合均匀,提高硅胶的物理性能。
- 挤出成型:将混合好的硅胶送入挤出机,通过模头成型。
- 后处理:包括冷却、切割、修整等步骤,确保最终产品的质量。
为了提高工艺效率,应注意以下几点:
- 混炼均匀:确保硅胶与添加剂充分混合,避免局部不均导致的产品缺陷。
- 温度控制:合理设置各段的温度,防止硅胶过早固化或分解。
- 压力调节:保持稳定的挤出压力,避免因压力波动导致的产品尺寸变化。
- 速度匹配:挤出速度应与冷却速度相匹配,确保产品在离开模具时已基本定型。
三、材料选择与改进
硅胶材料的选择直接影响挤出效率及产品质量。常见的硅胶材料有:
- 液体硅橡胶(LSR):具有流动性好、固化速度快的特点,适合精密部件的生产。
- 固体硅橡胶(HCR):硬度范围广,可塑性强,适用于多种应用场景。
针对不同需求,可通过以下方式改进材料性能:
- 添加填料:如二氧化硅、碳酸钙等,可提高硅胶的机械强度和耐磨性。
- 调整配方:通过改变硅胶的分子量分布、交联密度等参数,优化其流变性能。
- 表面改性:通过接枝、共聚等方法,改善硅胶的亲水性或疏水性,以满足特定的应用需求。
四、环境因素考量
硅胶挤出过程中,环境条件也会影响生产效率和产品质量。主要环境因素包括:
- 温度:保持车间内恒定的温度,避免因外界温度变化导致硅胶性能不稳定。
- 湿度:控制空气湿度,防止硅胶吸收过多水分,影响固化效果。
- 清洁度:定期清理设备和工作区域,避免杂质混入硅胶中,影响产品质量。
五、总结
硅胶挤出是一项技术含量较高的工艺,要实现高效挤出,需从设备选择、工艺流程优化、材料选择及环境控制等方面入手。通过综合考虑以上因素,不仅可以提高生产效率,还能保证产品质量,满足市场对高性能硅胶制品的需求。未来,随着新材料和新技术的发展,硅胶挤出工艺将进一步优化,为更多行业提供可靠的支持。
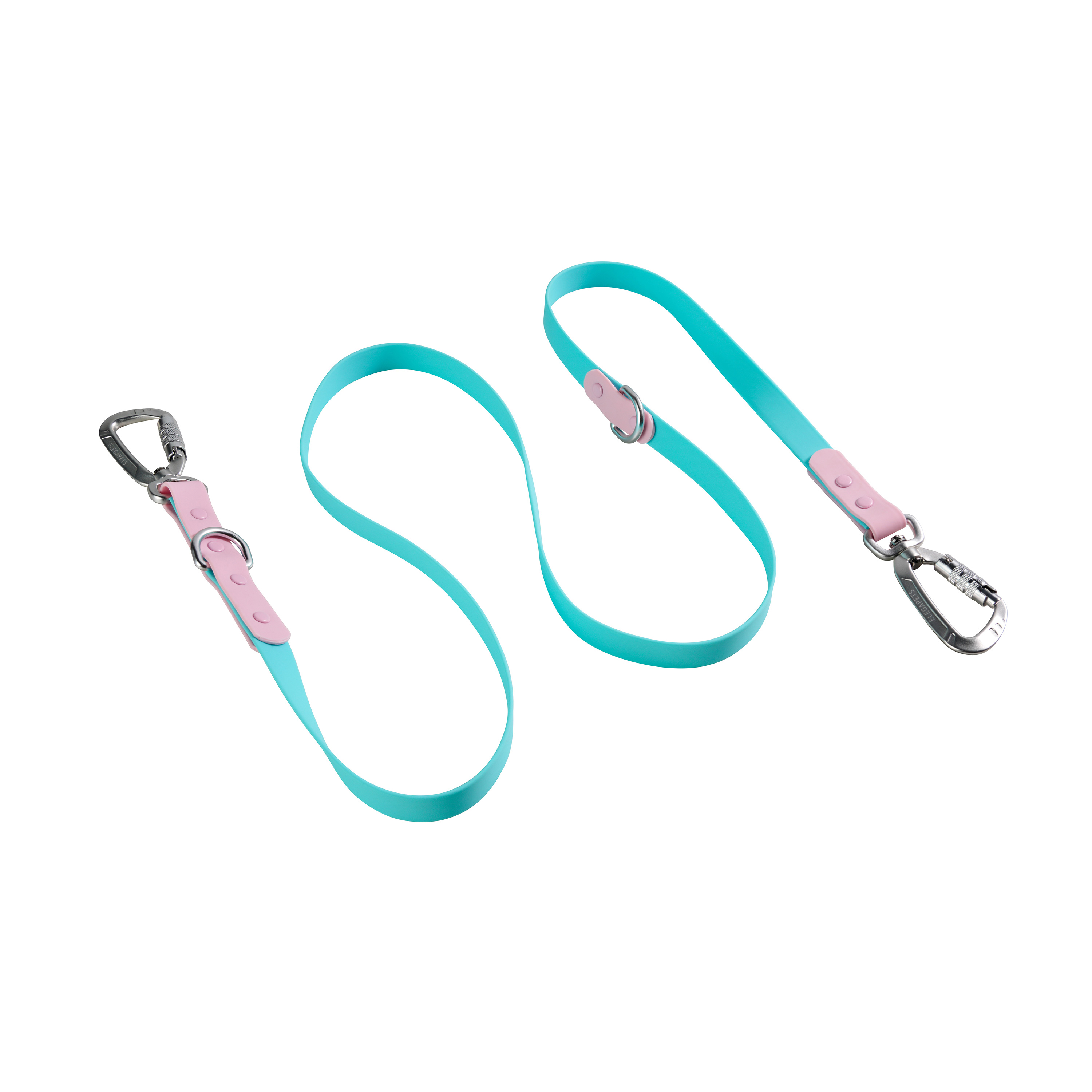