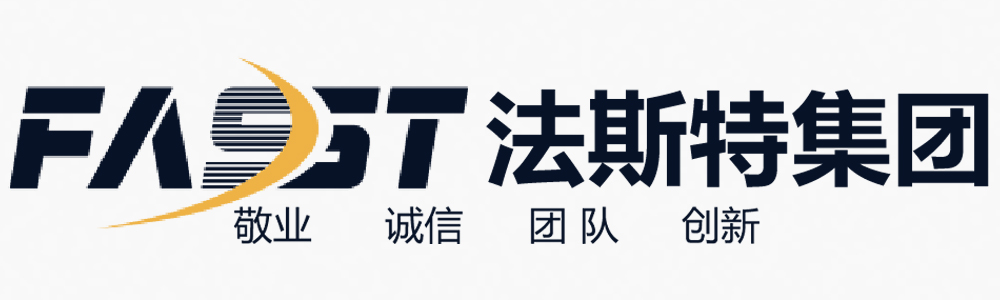
O型密封圈是广泛应用于各种机械、设备和管道系统中的重要密封元件。由于其结构简单、安装方便、密封效果好等特点,在工业生产中得到了广泛应用。然而,O型密封圈在实际应用过程中会遇到各种恶劣环境条件,如高温、高压、腐蚀介质等,这些因素会对密封圈的物理性能产生影响。其中,耐撕裂性能是衡量O型密封圈使用寿命和可靠性的重要指标之一。本文将探讨O型密封圈的耐撕裂性能及其影响因素。
O型密封圈通常由橡胶、塑料或金属材料制成。其中,橡胶材料因其良好的弹性和压缩变形能力而被广泛使用。常见的橡胶材料包括丁腈橡胶(NBR)、氟橡胶(FKM)、硅橡胶(VMQ)等。这些材料在不同温度和压力条件下具有不同的物理性能,从而影响到O型密封圈的整体性能。
耐撕裂性能是指材料抵抗撕裂破坏的能力。对于O型密封圈而言,耐撕裂性能直接影响其在使用过程中的稳定性和寿命。当密封圈受到外部力的作用时,如果其耐撕裂性能不足,则容易发生撕裂现象,导致密封失效,进而引发设备故障或安全事故。因此,提高O型密封圈的耐撕裂性能是确保其长期可靠运行的关键。
材料的选择对O型密封圈的耐撕裂性能至关重要。不同类型的橡胶材料具有不同的物理力学性能,如抗拉强度、断裂伸长率和撕裂强度等。例如,氟橡胶(FKM)因其优异的耐热性、化学稳定性和机械强度而被广泛应用于高温、高压及腐蚀性环境中;而硅橡胶(VMQ)则以其优良的耐寒性和生物相容性著称。选择合适的材料是保证O型密封圈耐撕裂性能的基础。
制造工艺对O型密封圈的耐撕裂性能也有显著影响。例如,硫化过程中的温度、时间和压力控制不当可能导致材料内部结构不均匀,从而降低其整体性能。此外,加工过程中的应力集中区域也可能成为撕裂的起点,因此需要严格控制加工参数以避免这些问题的发生。
O型密封圈的工作环境对其耐撕裂性能有着直接的影响。高温、低温、高压、腐蚀性介质以及机械振动等因素都可能加速材料的老化过程,导致其物理性能下降。例如,在极端温度下工作的密封圈可能会因为热膨胀系数差异而产生额外应力,从而增加撕裂的风险。因此,在设计阶段就需要充分考虑实际应用环境,并采取相应的防护措施来延长密封圈的使用寿命。
通过调整橡胶配方中各组分的比例,可以改善材料的物理性能。例如,添加适量的补强剂可以提高材料的抗拉强度和撕裂强度;加入防老剂则有助于延缓材料老化过程,从而提升其长期使用的稳定性。
采用先进的制造技术,如精密注塑成型技术,可以在保证产品质量的同时减少材料内部缺陷,提高成品的一致性和可靠性。同时,通过优化硫化条件,可以使材料达到最佳的物理状态,进一步增强其耐撕裂性能。
合理的设计能够有效分散作用于密封圈上的应力,防止局部应力集中导致的撕裂现象。例如,采用适当的倒角设计或增加加强筋等措施都可以显著提高密封圈的耐撕裂性能。
综上所述,O型密封圈的耐撕裂性能是确保其在复杂工作环境下长期稳定运行的关键因素之一。通过合理选择材料、改进制造工艺以及优化设计结构,可以有效提升O型密封圈的耐撕裂性能,从而延长其使用寿命并提高系统的安全性与可靠性。未来的研究方向应更加关注新型材料的研发以及先进制造技术的应用,以满足日益增长的高性能密封需求。
公司:惠州市法斯特精密部品有限公司
地址:龙门县惠州产业转移工业园北片区园区大道5号惠州市法斯特科技产业园区2号厂房四-五楼
Q Q:18665211415
Copyright © 2002-2024